Dry End Roll Handling br> Systems
Description
AHI’s Dry End Roll Handling System automates the roll, shaft, and core handling at the dry end of a tissue machine. Regardless of your manufacturing environment, Automatic Handling’s talented team of engineers can work with your team to customize the dry end production capabilities of your tissue manufacturing lines.
Applicable Industries
Tissue & Towel
System Highlights
- Automatically handles dry end parent rolls moving them to converting or storage
- Integrated shaft & core handling
- Fully integrated film wrapping for roll protection
- Stationary (non rolling) movement of soft tissue rolls to maintain roll integrity
How Dry End Roll Handling Systems work:
The system begins by lifting a full roll set, and shaft from the kitchen rails of the tissue machine engages the shaft end, deflates the shaft, and pulls the shaft from the roll set cores. The roll set is subsequently lowered and transferred from the machine area into the roll handling system. Here, the system introduces new cardboard cores into the machine, raises them, inserts the shaft into the core, inflates the shaft, and lowers the inflated shaft back down onto the kitchen rails for a new roll set. The parent rolls are either conveyed forward, inspected for separation, or pass through the roll breaking sequence before continuing onward.Each parent roll is individually weighed and automatically labeled on the bilge. After that, the rolls convey through a film wrapper where they can either pass straight through or be film-wrapped for shipping protection. Next, rolls are sent into a lowerator (if multiple floors) or directly into an upender machine that changes the roll position from horizontal to vertical. At this juncture, rolls are accumulated and conveyed to pick-up stations using either a clamp truck or Automatic Guided Vehicle. All roll data is tracked throughout the system and transferred to third-party networks as necessary.
The system receives cores from internal core racks and removable core bins and stores them internally in the core handling system while tracking dimensions and quantity in the PLC/HMI. Finally, cores are individually picked, conveyed, and delivered to the tissue machine to be mated back with the shaft. Rejected cores are transferred either to an internal core rack or to a position where operators can remove them safely.
Robotic Labeling Integration Enhancements
To enhance your dry end rolling handling automation, we offer an extensive variety of robotic labeling systems. These labeling systems can verify the product labeled and place the label in the correct position. Leveraging Collaborative Robots (Cobots) allows you to run in a fully automatic mode or a manual mode where the cobots interact with humans in a shared workspace.
In the event your operations require more complex labeling applications, we have numerous inline and end-of-line mechanical roll label application solutions that we have developed for the tissue, paper, film, foil and agricultural industries.
A Dry End Roll Handling System in factory acceptance testing at AHI
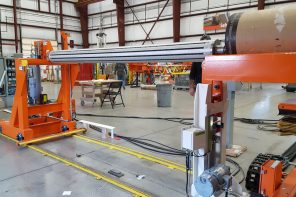
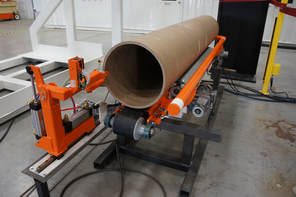
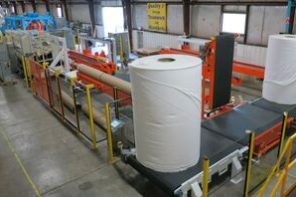
Dry End Roll Handling Systems we've Built
Below are examples of Dry End Roll Handling Systems we have customed designed to our clients’ needs. Each system is optimized to deliver the required through-put while maintaing safety and reliability.
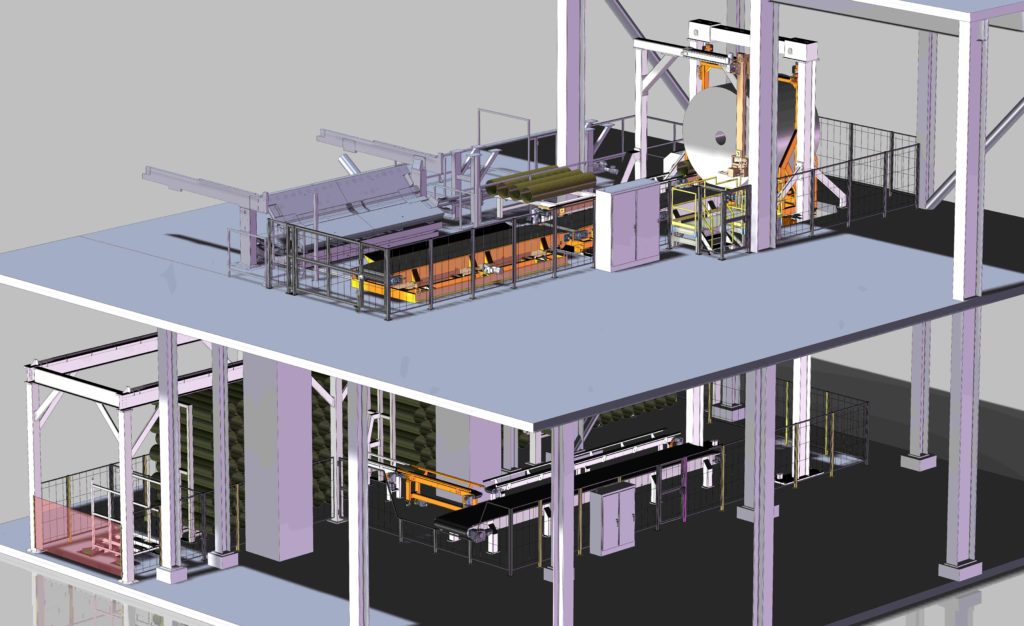
Example System 1
This dry end roll handling system demonstrates our ability to design, build, and manufacture systems to your operational needs.
- Core delivery & parent roll pickup
- AGV Interface on both core and roll ends
- Automatic Core Storage & Delivery
- Lowerator for multi floor operation
Example System 2
- Lowering scoop for reject roll set
- Vertical Roll Wrapper
- Automatic Core Storage & Delivery
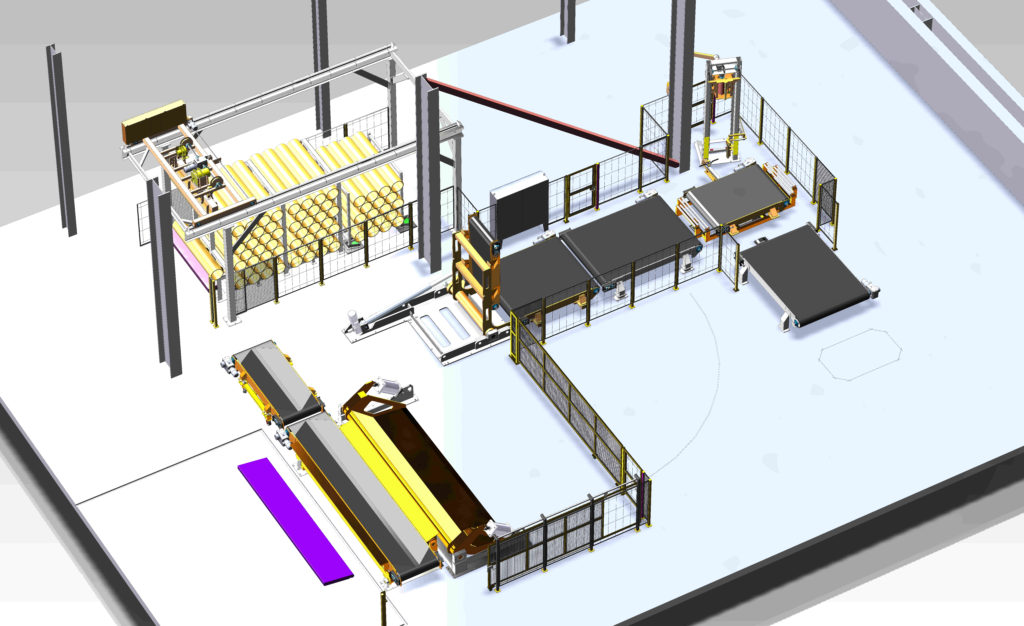
Auto InFlate and DEFLATE for CORE HANDLING
Automatic Handling offers automated core management equipment and systems. Our Auto Inflate and Deflate technology allows your company to modernize their operations and replace the need for manual inflation and deflation of shafts.
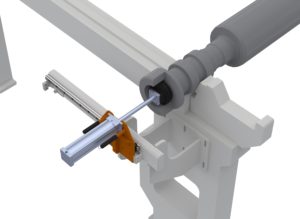
Related Systems
Ready to Automate?
We have the knowledge and expertise to automate your manufacturing process and build the custom equipment support your facilities unique needs.